Zelma George Recreation Center is a focal point in the residential Cleveland neighborhood where it is located. It houses a basketball court, a roller rink, exercise areas and a running track. Surrounding the building are trees, baseball fields, and an outdoor track. The center has a park-like atmosphere and constantly is being utilized by the families in the area.
Because it is such a highly used facility, it is important the building perform properly, as well as be aesthetically pleaseing. After 10 years, the building still looked good, but some issues had arisen. The original metal roof was not watertight and had leakage problems. The panel profile used was not adequate for this type of application. The city needed to find a solution.
Let It Rollform
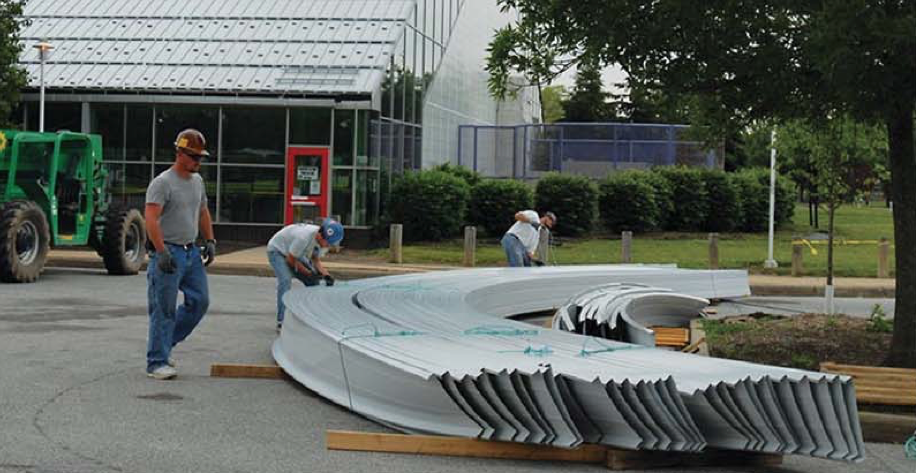
Commercial Siding, Painesville, Ohio, (update: now Houston) has been involved with metal roofing and siding projects since 1960. It has undertaken reroofing projects nationally for 25 years and also has years of experience doing flat-to-slope conversions and metal-over-metal overlay systems over existing roofing. The company has done millions of square feet of projects for the military and government.
In addition to installing metal panels, Commercial Siding rollforms its own standing seam panels using on-site rollformers. The contract belongs to the 15-member, East Baton Rouge, LA.-base Ultra Seam Association Inc. The members get tests from Camas, Wash.-based Underwriters Laboraties and West Conshohocken, PA.-based ASTM International and market their panels as a group. Making and installing its own panels helped allow Commercial Siding to come in with a bid 30 percent lower than its competitors for the Zelma George project.
Although the roof was leaking and needed to be fixed as quickly as possible, the city of Cleveland’s engineers and the team as a whole new it would best not to start the project during a rough Midwest winter. The project waited until spring 2008. “[The engineers agreed] with our opinion, which was that we can do this job during the winter and all be unhappy or we can wait and let Mother Nature calm down a little bit so we can do a good job,” says Tim Lane, Commercial Siding’s president, who has been with the company for 34 years. “They were patient enough to [wait].”
Making Panels
The building has an interesting configuration with an elliptical barrel roof in the center and straight roof slopes coming off the two sides. There is more than 50,000 square feet (4645 m2) of roofing area, so the team felt the best solution was to form the roof panels on-site. Commercial Siding used 24-gauge Galvalume-coated steel coil with a white PVDF finish.
Quite frankly, due to the size of the sheets, I don't think you could have done it any other way; particularly the radiussed ones. So I think that was a huge advantage. I don't know how you could have done this using factory-rolled panels without having some splices in it.
The metal was formed into 16-inch- (406mm-) wide standing seam roof panels. A rollformer was used for panel fabrication and the panels were curved on site as well. Some of the radiussed panels were up to 60 feet (18m) in length with an arch of 10 to 12 feet (3 to 3.7 m). Lane felt forming the panels on site was the key to having a quality product. “Quite frankly, due to the size of the sheets, I don’t think you could have done it any other way; particularly the radiussed ones,” he comments. “So I think that was a huge advantage. I don’t know how you could have done this using factory-rolled panels without having some splices in it.”
Although the panels weren’t heavy, their size made it difficult to get them to the roof surface. “Probably the biggest challenge was getting a quality product rolled and up on the roof still in A-1 condition so it can be installed and look great when the job is done,” Lane recalls. Even with the challenge, he had faith in his crew. “Our foreman and crew have been with us for years so I think, from a skill standpoint, our field people are unmatched. There are a few things out there we haven’t seen yet, but not a lot.”
Once all the panels were rolled, they were set aside so the crew could make a device to get them on the roof. What they developed was a beam curved to the same radius as the roof panels with stirrups along the radius. The panels were loaded on the right and left of the beam so it was balanced. The loaded beam was lifted by crane to the roof. “We like to engineer things and make every job its own, fun project,” Lane says. “Our guys are good problem solvers.”
We like to engineer things and make every job its own, fun project. Our guys are good problem solvers.
Before the panels were to be installed, a reroof framing system was installed over the existing metal roof. The rollformed metal pieces have custom divots punched out so they can be used over any metal roof system. The framing also makes the building stronger by enhancing the existing structure.
Beautiful and Functional Again
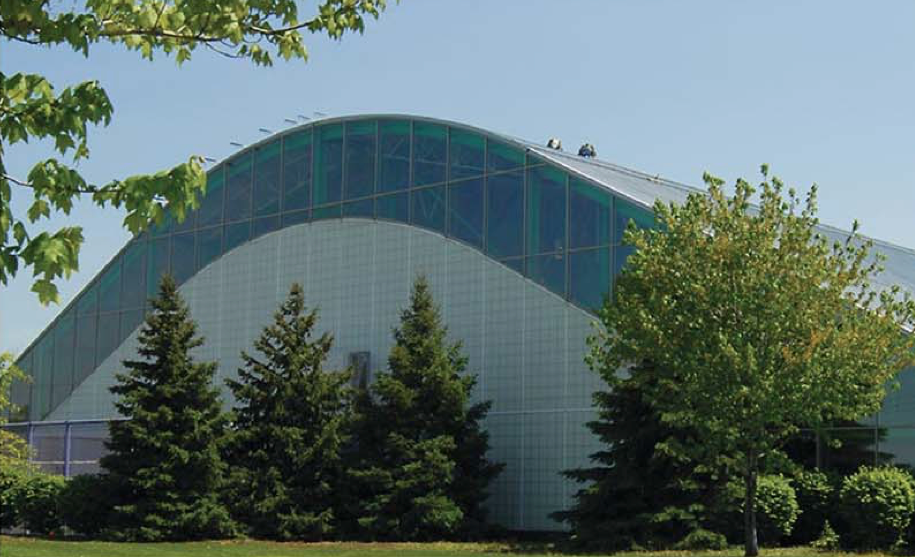
The project was finished in early summer 2008. The installation device the Commercial Siding crew made kept the panels free of dents and scratches, which was crucial for this project. “When we are done, the panels looked great and that’s one of the most important things because it is a high-visibility project,” Lane says. “It has to perform, but it also has to look great.”
Unlike its predecessor, the new roof is performing well. There have been no problems at this point. Lane has taken great pride in the finished product. “It’s a focal point in the neighborhood. When you drive by it looks great and it’s performing well.” Now the building is a match for the high-performance athletes who use it.
Krista Hovis writes about architecture and metal construction from Kansas, Ohio.
The original PDF of this article appeared in the June 2009 issue of MetalMag and can be found here.